Functional Thermoplastics
Polymer materials can be optimised for processing and application through additives and other polymers. As a result, they can be made to meet the most demanding requirements and enable entirely new areas of application. However, they also require an in-depth understanding of the interplay between structure, processing, and properties, as they are typically multi-phase materials.
We research the targeted adjustment of the properties of thermoplastic materials. These functional thermoplastics are characterised by unique thermal, electrical, optical, mechanical, or processing properties. The use of such materials in additive manufacturing and other integrative manufacturing processes is particularly important to us.
Selected fields of application for our research
- Transport
- Energy technology
- Medicine technology
- Electric & electronics
The combination of two or more polymers into polymer blends makes it possible to combine the outstanding property profiles of the individual polymers. In this way, novel polymers are created that allow innovative applications and processes to be established.
The main focus of our research activities is on thermoplastic blends. Depending on the requirement profile, we combine polymer materials ranging from standard thermoplastics such as polyolefins, to technical thermoplastics such as polyamides and polycarbonates, to high-performance thermoplastics such as polyetherimide.
Properties such as improved mechanical resistance at elevated temperatures or under the influence of media, optimised thermal conductivity for applications in energy technology, or improved optical transparency are just some of our research topics. This is achieved through the targeted adjustment of the physical and chemical composition of the blends on the one hand, and the selection of suitable processing methods on the other. The methods used range from the synthesis of suitable compatibilisers by reactive extrusion, to the use of commercial copolymers as processing additives, to influencing molecular weight with low-molecular, reactive compounds. In addition, we simulate processing parameters in compounding extruders in order to produce customised polymer systems. The excellent equipment at Polymer Engineering allows us to develop polymer blends up to a pre-industrial size scale, and to characterise their properties morphologically, rheologically, thermally, and mechanically.
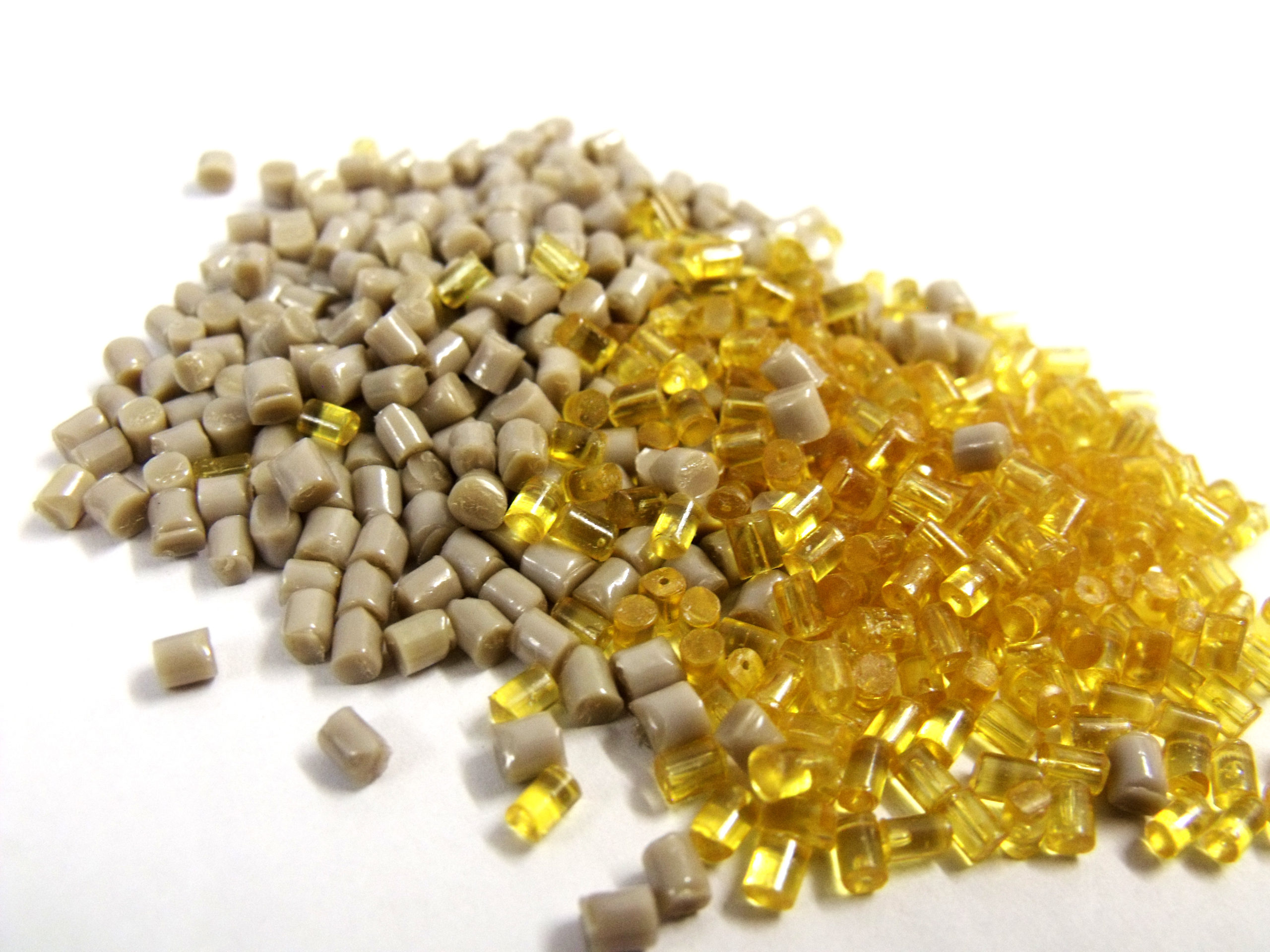
Printed circuit boards
Whether laptop, smartphone, or antenna and radar technology in the high-frequency range – electronic products have become indispensable companions. A core component for these products is the PCB substrate, which forms the basis for electronic circuits and components. A variety of thermoplastic polymers already meet several requirements for this application, and enable highly economical processing using conventional methods such as extrusion or injection moulding. However, it is necessary to meet further requirements such as a low coefficient of thermal expansion, low loss factors, and low dielectric constants.
We are therefore developing new classes of thermoplastic printed circuit boards based on high-temperature thermoplastics. Thermoplastic substrate materials have several advantages over traditional PCB substrates. In particular, continuous processing opens up the possibility of developing single-stage, highly automated processes starting with the raw materials all the way to the double-sided copper-clad PCB, which can lead to significant cost reductions. In addition, most high-temperature thermoplastics do not require additional flame retardants to meet flame resistance requirements as they are inherently flame retardant. They are also fully material recyclable thanks to their chemistry. In addition, thermoplastic PCBs offer the possibility of three-dimensional forming, allowing the PCB to adapt to ever-shrinking installation space.
Two generations of thermoplastic PCB, foamed and highly filled, have been developed so far. They have proven their utility and competitiveness compared to commercially available substrates in the shape of functional demonstrators. Due to their thermoplastic properties, these substrates offer an innovative possibility to generate environmentally-friendly high-performance electronics for the future.
Insulator materials
In electrical and power engineering, the performance of a component is largely determined by its electrical properties. Polymer materials are known for their good electrical insulation properties. While the field of cable insulation is dominated by thermoplastic polymers such as PP, PVC, or cross-linked PE, epoxy resin-based insulation systems are used especially for the insulation of high-voltage generators and transformers. We have several years of experience in researching innovative insulation systems for high-performance generators.
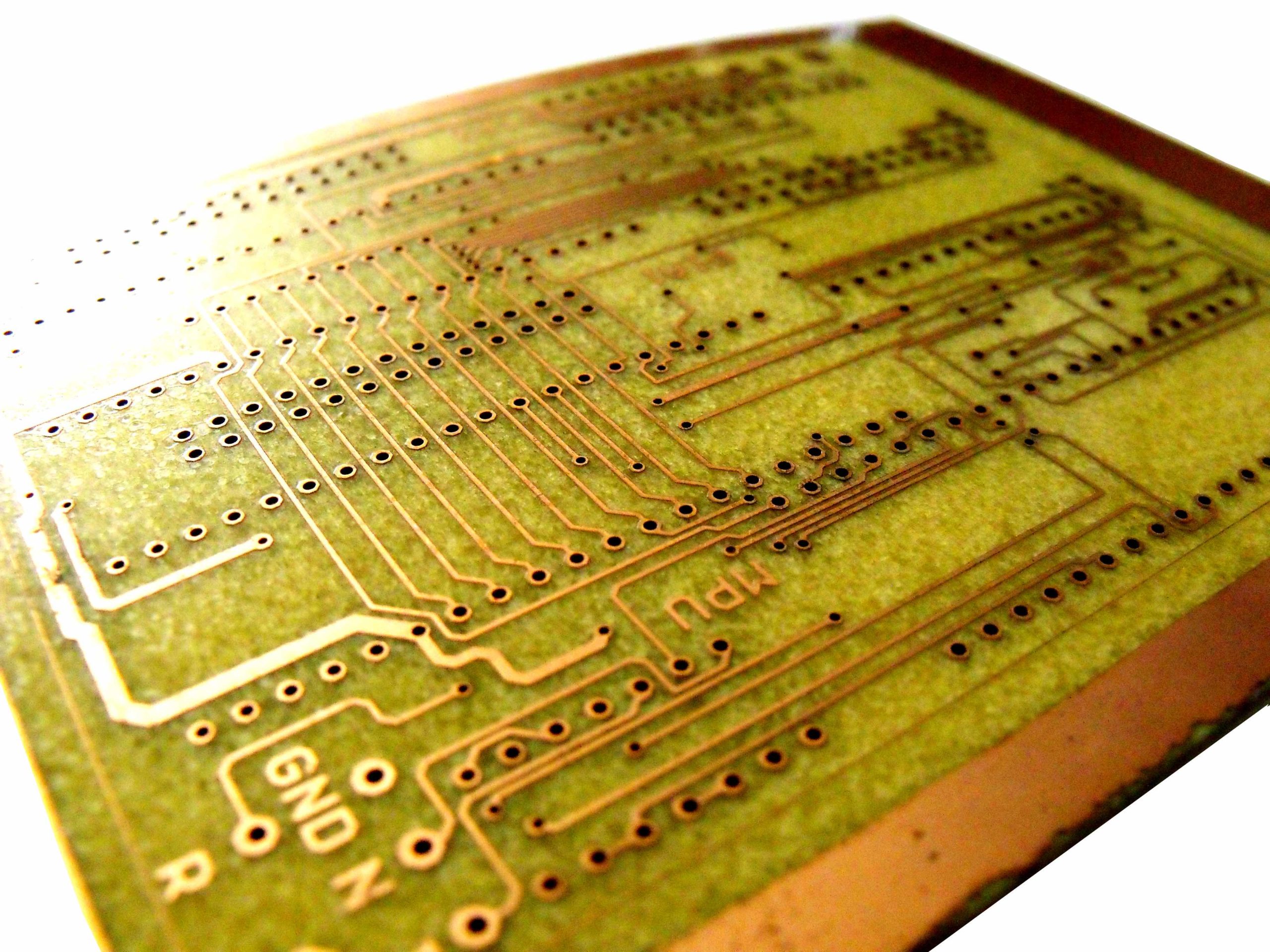
The use of very small quantities of additives in just the nanometre range (< 100 nm) allows for significant improvement in the initial properties of polymer materials, such as their mechanical characteristics, barrier properties, or flame resistance. Currently, there are intensive efforts underway worldwide to develop and test so-called nanocomposites with a wide variety of nanoscale additives (e.g. layered silicates, spherical silicate particles, carbon nanotubes, and carbon nanofibres). Despite some industrial successes already achieved in the development of polymer nanocomposites, the focus remains on basic research.
The introduction of nanoscale fillers into polymer matrices can have significant effects on both the processing behaviour and the internal structure (morphology) of polymer materials. By skilful selection of material components and manufacturing processes, such effects can be used to produce even the most filigree components with optimised property profiles.
We are currently working on the development of nanocomposites based on mineral nanofillers (layered silicates, halloysites, silicate particles) and carbon-based additives (CNTs, graphene, carbon black). Halloysites have a similar chemical structure to phyllosilicates, but are in the form of tubes. These nanoparticles are of natural origin, and due to their high aspect ratio, are promising candidates for increasing the stiffness and strength of polymers. Carbon-based nanofillers such as carbon black (CB), carbon nanotubes (CNT), carbon nanofibres (CNF), or graphene (GNP) are used to influence the properties of compact polymer matrices as well as foams. These include properties such as electrical and thermal conductivity, or static and dynamic mechanical properties.
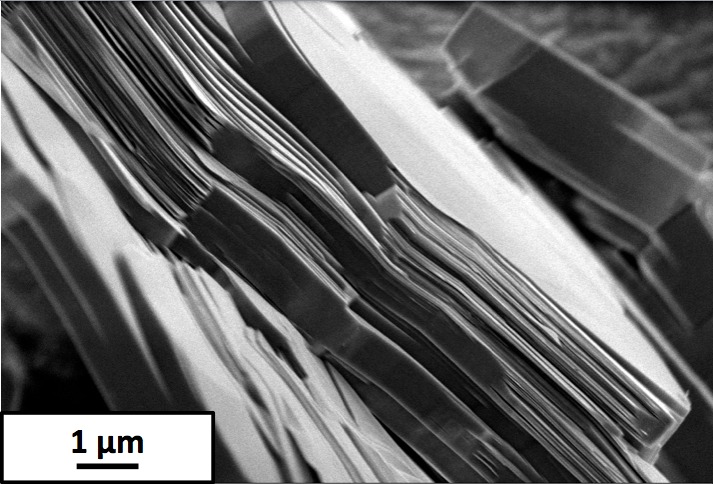
Thermoplastic elastomers (TPE for short) combine the advantages of thermoplastics and elastomers in equal measure. They can be melted and thus reshaped almost as often as desired – and are nevertheless permanently elastic again afterwards. Today, there is a wide range of TPEs, such as TPU, TPA, TPO and TPE-E. Although thermoplastic elastomers were already developed around 1950, industrial series production did not start until the 1970s. Through constant further development, thermoplastic elastomers can now be regarded as a fully-fledged class of materials.
TPEs consist of a soft (amorphous) and a hard (crystalline) segment, which results in the respective properties being evident in their elastic and thermoplastic behaviour. The use of TPEs offers the following advantages:
- Thermoplastic processing
- Short production cycles
- Low energy consumption
- Integral component concepts through multi-material use
- Recyclability
- Ease of colouring
Despite the advantages mentioned, some factors must always be taken into account when using them:
- Crystallinity of the hard segment
- The thermal characteristics and thermal stability of both segments
- Processing temperatures, which depend on the hard segment
- Rheological behaviour of the TPE
Through many years of research on TPEs, we have a broad understanding of the processing of TPE composites and foams. For example, foam extrusion of TPEs has gained in importance over recent years, and is a special research focus for us. We have the know-how to tailor the cell morphology and thus the mechanical properties of TPE foams. Furthermore, we have experience in working with reactive and neutral additives that can be incorporated via the extrusion process.
The additivation of polymers is indispensable in order to adapt their properties to the requirements placed on them. Additives are essential in the processing of plastics, open up new areas of application, and guarantee the properties desired to the end user. The stability of polymers and the mechanical, electrical, and optical properties can be improved effectively by novel additives, and equally, special polymers can be developed displaying unique property profiles.
Among other things, we are working on controlling the morphology of semi-crystalline polymers by processing them with novel additives that act as nucleating agents for polymer crystallisation when the polymer melt cools. By using such nucleating agents and optimising processing conditions, the crystallisation behaviour of the polymer solid and thus its properties can be influenced.
In addition to controlling morphology, functionalising the charge properties of a polymer is also a highly exciting field of research. Electrets are materials that are suitable for storing electrical charges over a long period of time. Such materials are mainly used as microphones and as filter media. Research in this field at Polymer Engineering is concerned with the development and characterisation of certain new polymer electrets made of various polymer blends/additives. For this purpose, electrets with exceptional charge stability based on polypropylene (PP), polyetherimide (PEI), polyphenylene ether (PPE), and the appropriate blend materials are being developed. The materials are charged by corona treatment (for films and foams) or electrospinning (for fibres), and subsequently evaluated for long-term and/or temperature stability of charge. The improvement of charge storage properties is achieved by the addition of additives and/or by variation and adaptation of morphology. Porous polymers with high anisotropy (see figure) show a significant improvement in electret properties, as the pores act as a barrier to charge carrier movement.
